Robotic Moving ‘Crew’ Preps for Work on Moon
As NASA moves forward with efforts to establish a long-term presence on the Moon as part of the Artemis campaign, safely moving cargo from landers to the lunar surface is a crucial capability. Whether the cargo, also known as payloads, are small scientific experiments or large technology to build infrastructure, there won’t be a crew […]
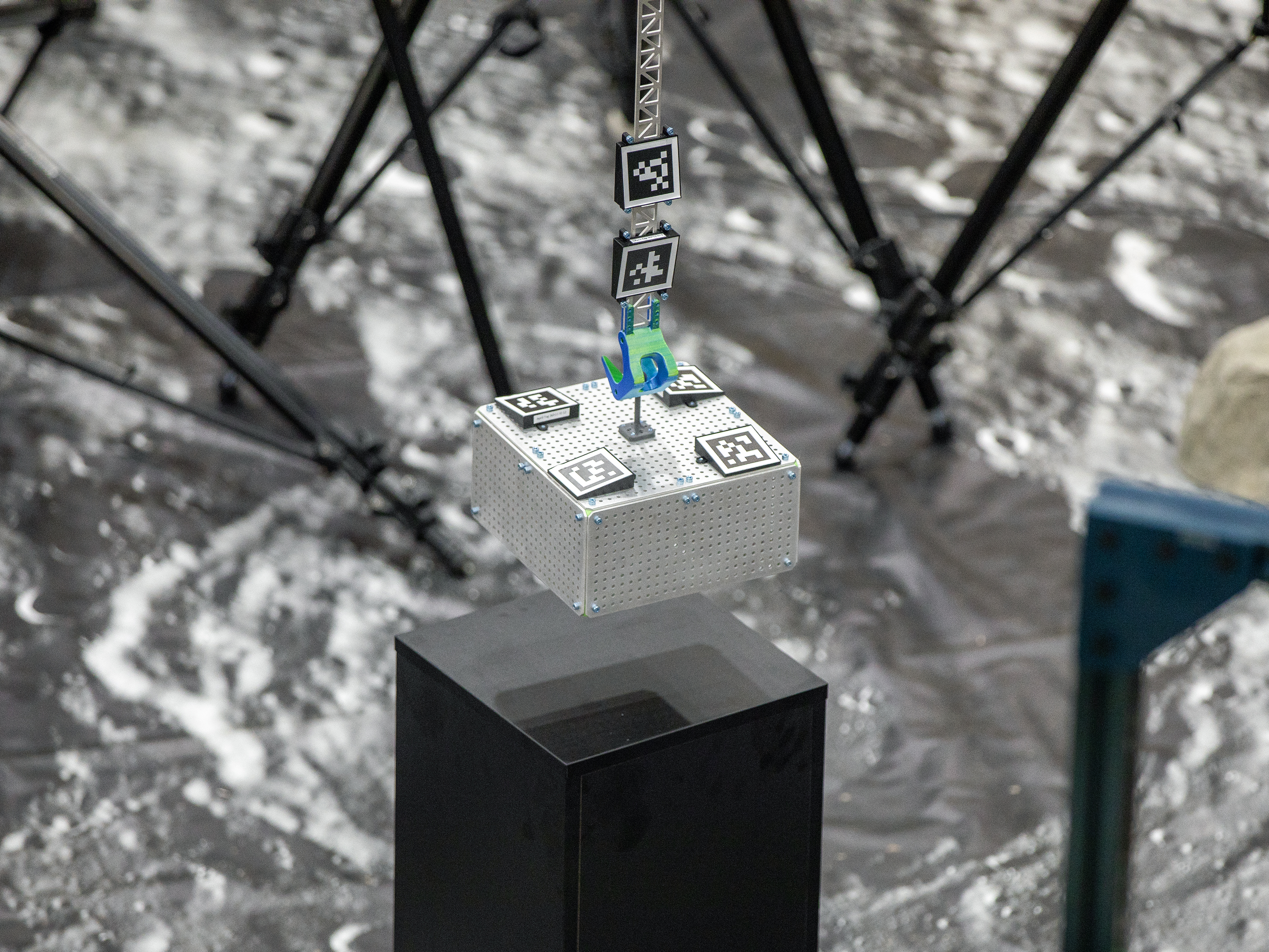
Robotic Moving ‘Crew’ Preps for Work on Moon
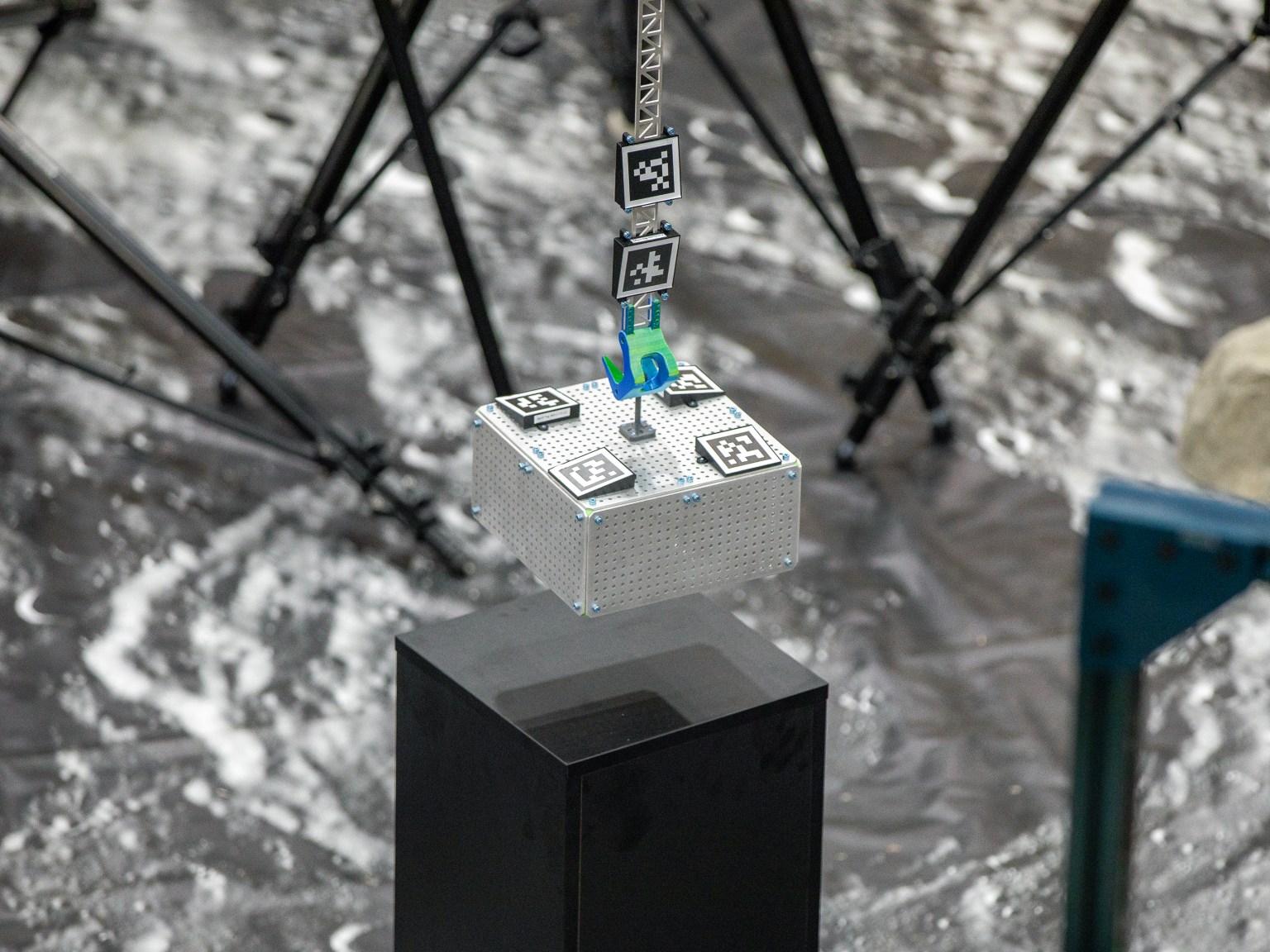
As NASA moves forward with efforts to establish a long-term presence on the Moon as part of the Artemis campaign, safely moving cargo from landers to the lunar surface is a crucial capability.
Whether the cargo, also known as payloads, are small scientific experiments or large technology to build infrastructure, there won’t be a crew on the Moon to do all the work, which is where robots and new software come in.
A team at NASA’s Langley Research Center in Hampton, Virginia, spent the last couple of years infusing existing robotic hardware with a software system that makes the robot operate autonomously. Earlier this month, that team, led by researcher Dr. Julia Cline of NASA Langley’s Research Directorate, ran demonstrations of their system called LANDO (Lightweight Surface Manipulation System AutoNomy capabilities Development for surface Operations and construction).
The demos took place in an area set up to look like the Moon’s surface, complete with fake boulders and a model lunar lander. During the first demo, the team placed the payload, a small metal box, on a black pedestal. The robotic arm stretched over the scene, with its dangling hook poised to grasp the box.
As the team huddled nearby around computers, sensors on the arm scanned the surrounding area, looking for the metal box, which was outfitted with encoded markers — similar to QR codes — that revealed critical information about its position and orientation relative to the arm. Using a graphic user interface, team member Amelia Scott also chose a location for LANDO to place the payload.
After locating the metal box and computing a safe path to move it, the arm began a slow, deliberate movement toward its target, coming in at a precise angle that allowed the hook to select a capture point on the payload. Once engaged, the arm slowly lifted the payload from the pedestal, moved right, and gently lowered the payload to the simulated lunar surface. With the payload safely on the surface, the system carefully disengaged the hook from the capture point and returned to its home position. The entire process took a few minutes. Shortly after the first demo was complete, the team did it again, but with a small model rover.
“What we demonstrated was the repeatability of the system,moving multiple payloads to show that we’re consistently and safely able to get them from point A to point B,” said Cline. “We also demonstrated the Lightweight Surface Manipulation System hardware – the ability to control the system through space and plan a path around obstacles.”
The system’s successful performance during the September demonstration marks the end of this project, but the first step in developing a larger system to go to the Moon.
Now that the team has determined how the system should function, Cline believes the next natural step would be to develop and test an engineering design unit on one of the landers going to the Moon as part of NASA’s Commercial Lunar Payload Services (CLPS) initiative. The team is actively looking for industry partners who want to commercialize the capability.
Through CLPS, NASA is working with commercial companies to deliver science and technology demonstrations to the Moon.
The work behind LANDO could be directly infused into much larger versions of a lightweight surface manipulation system.
“The overall control system we’ve developed would apply to larger versions of the technology,” said Cline. “When you think about the payloads we’ll have to offload for on the Moon, like habitats and surface power systems, this is the kind of general-purpose tool that could be used for those tasks.”
The LANDO system was funded through the Early Career Initiative in NASA’s Space Technology Mission Directorate (STMD). Through STMD, NASA supports and develops transformative space technologies to enable future missions. As NASA embarks on its next era of exploration with the Artemis campaign, STMD is helping advance technologies, developing new systems, and testing capabilities at the Moon that will be critical for crewed missions to Mars.
What's Your Reaction?
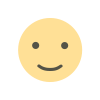
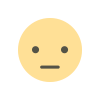
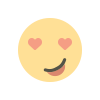
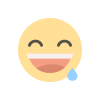
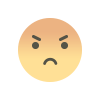
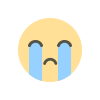
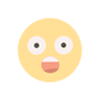