NASA Uses Small Engine to Enhance Sustainable Jet Research
Located inside a high-tech NASA laboratory in Cleveland is something you could almost miss at first glance: a small-scale, fully operational jet engine to test new technology that could make aviation more sustainable. The engine’s smaller size and modestly equipped test stand means researchers and engineers can try out newly designed engine components less expensively […]
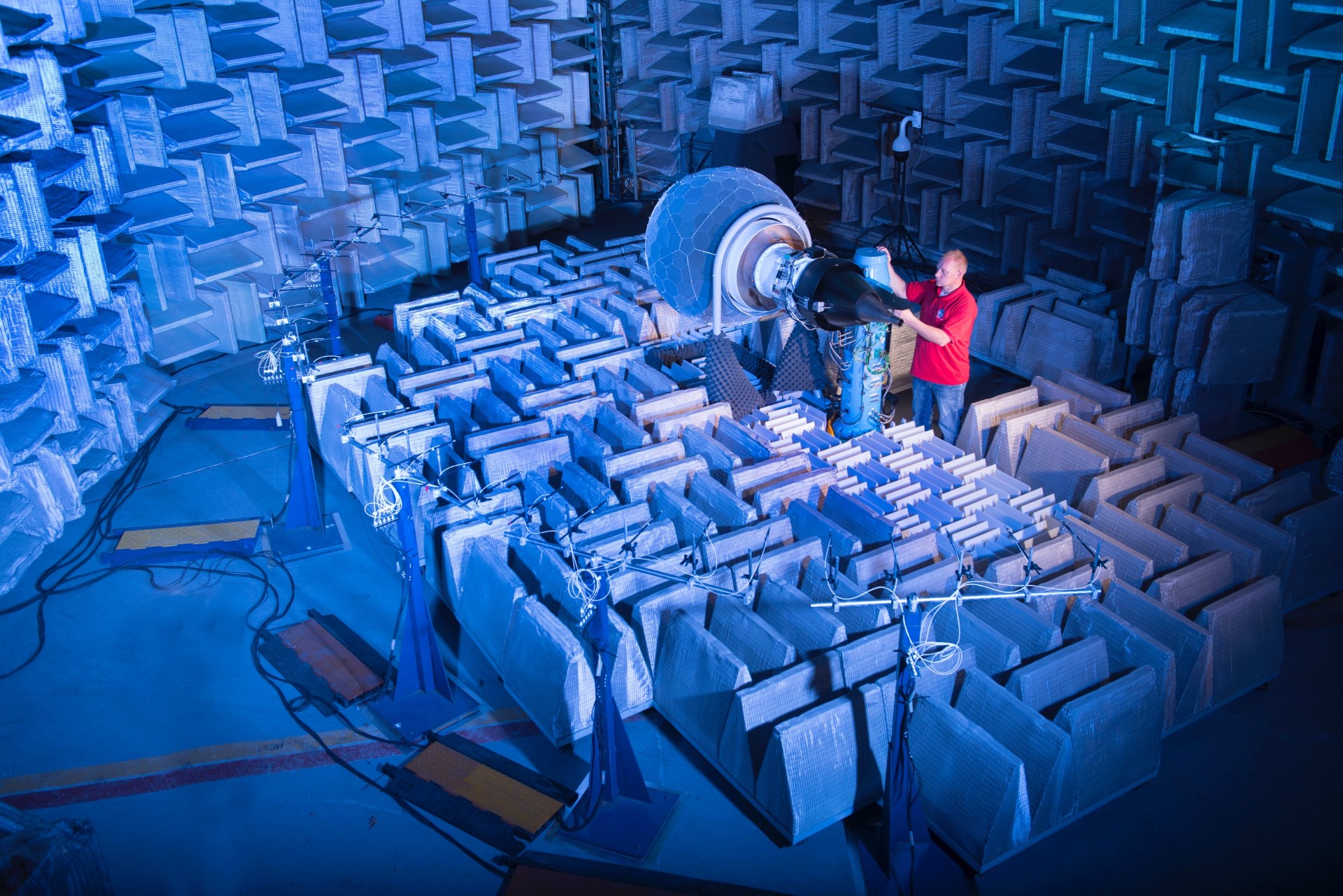
3 min read
Preparations for Next Moonwalk Simulations Underway (and Underwater)
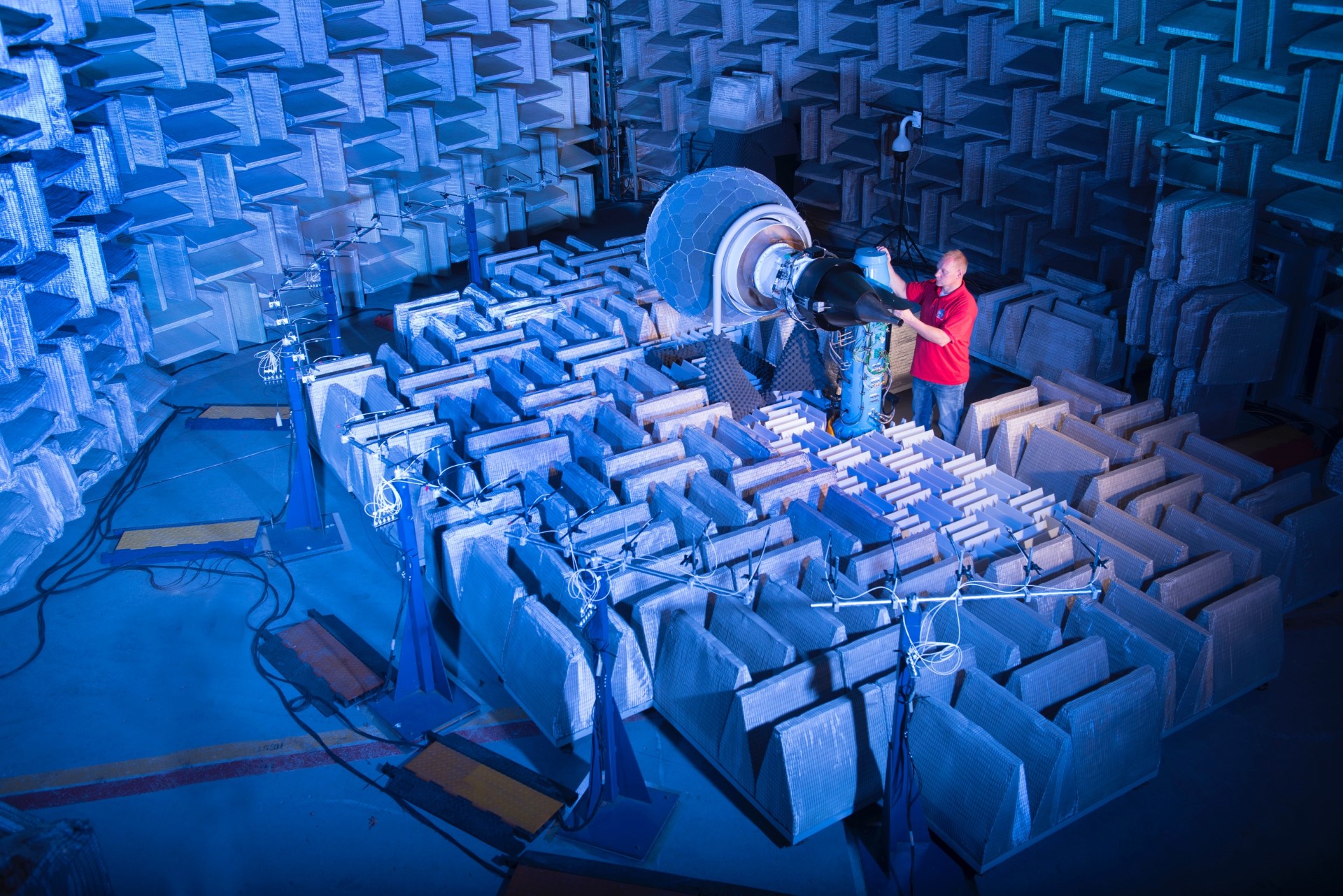
Located inside a high-tech NASA laboratory in Cleveland is something you could almost miss at first glance: a small-scale, fully operational jet engine to test new technology that could make aviation more sustainable.
The engine’s smaller size and modestly equipped test stand means researchers and engineers can try out newly designed engine components less expensively compared to using a more costly full-scale jet engine test rig.
Named DGEN380 Aero-Propulsion Research Turbofan, or DART, the engine is tiny enough to fit on a kitchen table, measuring at just 4.3 feet (1.3 meters) long. That’s about half the length of engines used on single-aisle airliners.
DART – not to be confused with NASA’s asteroid redirect mission of the same name – enables the agency to boost its sustainable aviation technology research because of its accessibility.
A hidden gem located inside the Aero-Acoustic Propulsion Laboratory at NASA’s Glenn Research Center in Cleveland, the DART engine was made by a French company named Price Induction (now Akira) and was acquired by NASA in 2017.
“DART’s small size makes it appealing,” said Dan Sutliff, who coordinates research for the engine at NASA Glenn. “It’s a great way to explore new technology that hasn’t yet reached the level of a full-scale operation.”
Small Steps Towards Big Goals
Several key NASA activities studying jet engines used DART in the past.
For example, it helped researchers learn more about incorporating materials that can help reduce engine noise. These technologies could be incorporated for use in next-generation airliners to make them quieter.
Now, NASA researchers plan to use the DART engine to investigate ideas that could help develop new ultra-efficient airliners for use during the 2030s and beyond. If all goes well, the technology could proceed to more exhaustive tests involving larger facilities such as NASA’s wind tunnels.
“DART is a critical bridge between a design and a wind tunnel test,” Sutliff said. “Technologies that work well here have a greater chance of achieving successful inclusion on future aircraft engines. The test rig helps NASA save resources and contribute to protecting our environment.”
Among its features, DART has a high bypass ratio, which is a measure of how much air passes through the turbofan and around the main core of the engine as opposed to entering it. Having a high bypass ratio means that DART is more characteristic of larger high-bypass ratio engines on commercial aircraft.
This design is more fuel efficient than other jet engines and makes DART ideal for testing new propulsion methods alongside NASA’s efforts in developing a small-core, fuel efficient jet engine for commercial airliners in the 2030s.
The DART engine also can test many other aspects of a jet engine including engine noise, operating controls, coatings used to protect engine parts, sensors and other instrumentation, and much more.
More information can be found on NASA’s Aero-Acoustic Propulsion Laboratory webpage.
Share
Related Terms
What's Your Reaction?
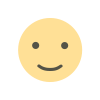
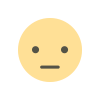
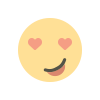
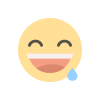
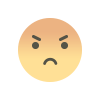
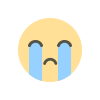
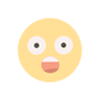